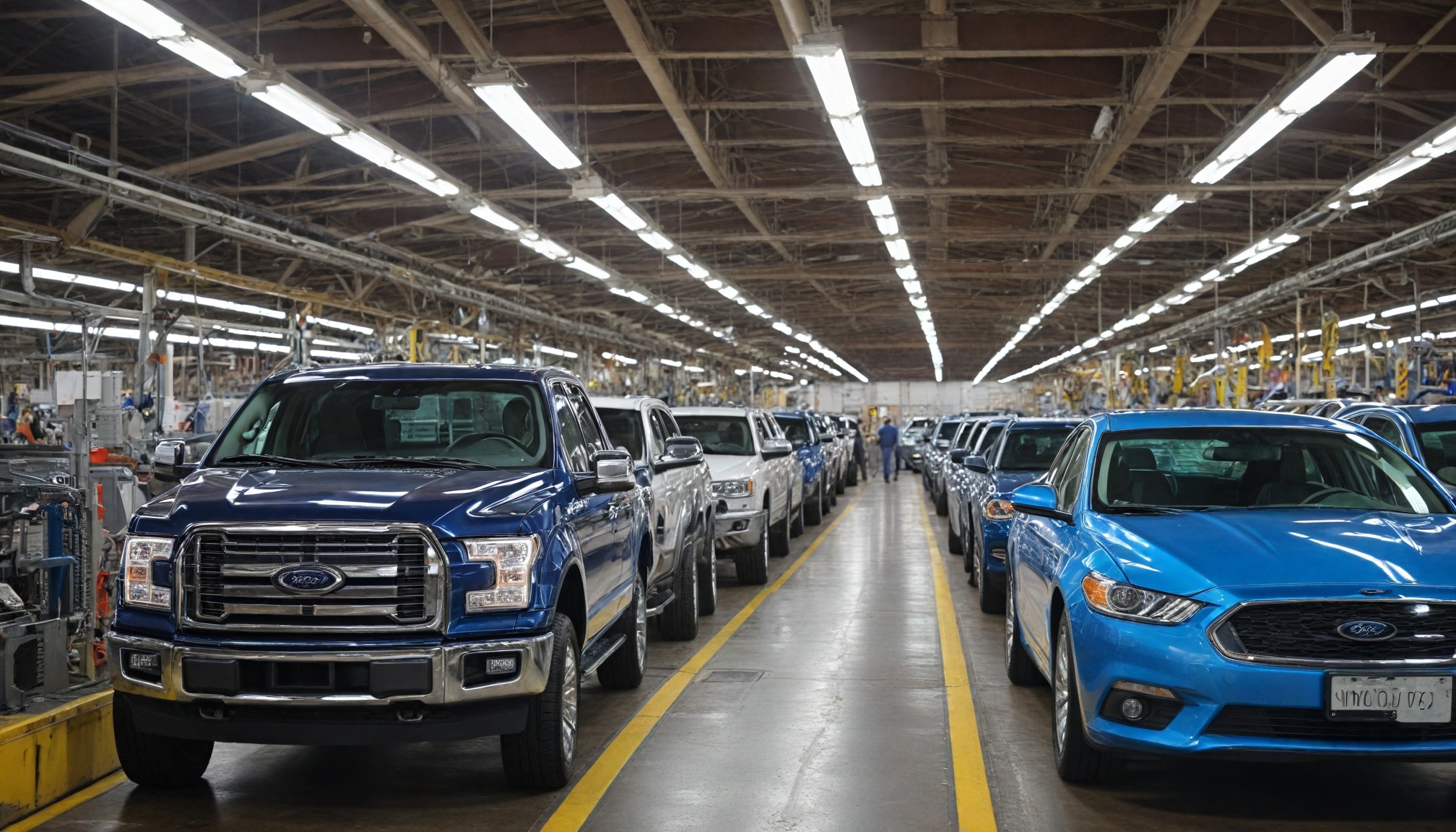
U.S. auto industry faces critical supply crisis as manufacturers rely on imported parts, with some components entirely unavailable domestically, creating economic and security vulnerabilities.
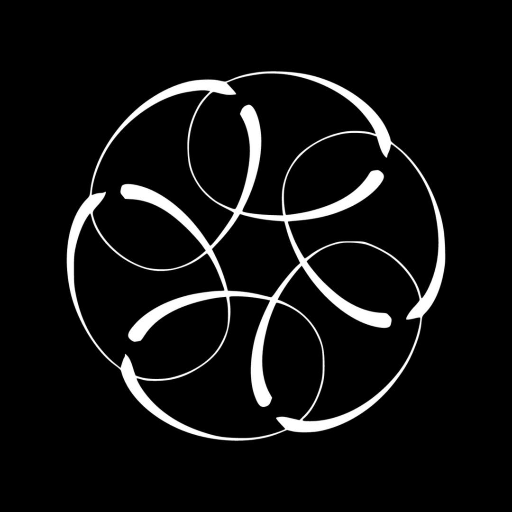
Drivetech Partners
The U.S. automotive industry faces an unprecedented dependency crisis as manufacturers increasingly rely on imported components for vehicle production. Ford's CEO's recent admission that certain critical components simply cannot be sourced domestically highlights a fundamental weakness in America's automotive manufacturing base, creating both economic and national security vulnerabilities.
Key Takeaways
Ford and other U.S. automakers face critical supply gaps with some components entirely unavailable from domestic sources
Nearly 50% of U.S. automotive parts imports come from Canada and Mexico, creating deeply integrated cross-border dependencies
Asian competitors like Japan and South Korea maintain significantly lower import reliance for their manufacturing operations
Proposed tariffs of up to 25% could increase vehicle costs and disrupt production networks throughout North America
The automotive industry contributes $1.2 trillion to the U.S. economy, making supply chain vulnerabilities a national economic concern
The Domestic Manufacturing Gap: Critical Components Unavailable in America
The situation facing U.S. automakers has reached a critical inflection point. Ford's CEO has publicly acknowledged that certain essential components simply cannot be sourced domestically at all. This isn't merely a cost issue but represents a complete absence of manufacturing capability within American borders. The stark reality reflects decades of shifting production patterns and deepening integration with global supply networks.
What makes this particularly concerning is that these aren't optional upgrades or specialty parts—they're fundamental components necessary for vehicle production. Without these parts, assembly lines stop, production schedules fail, and the economic ripple effects spread throughout the manufacturing sector and beyond.
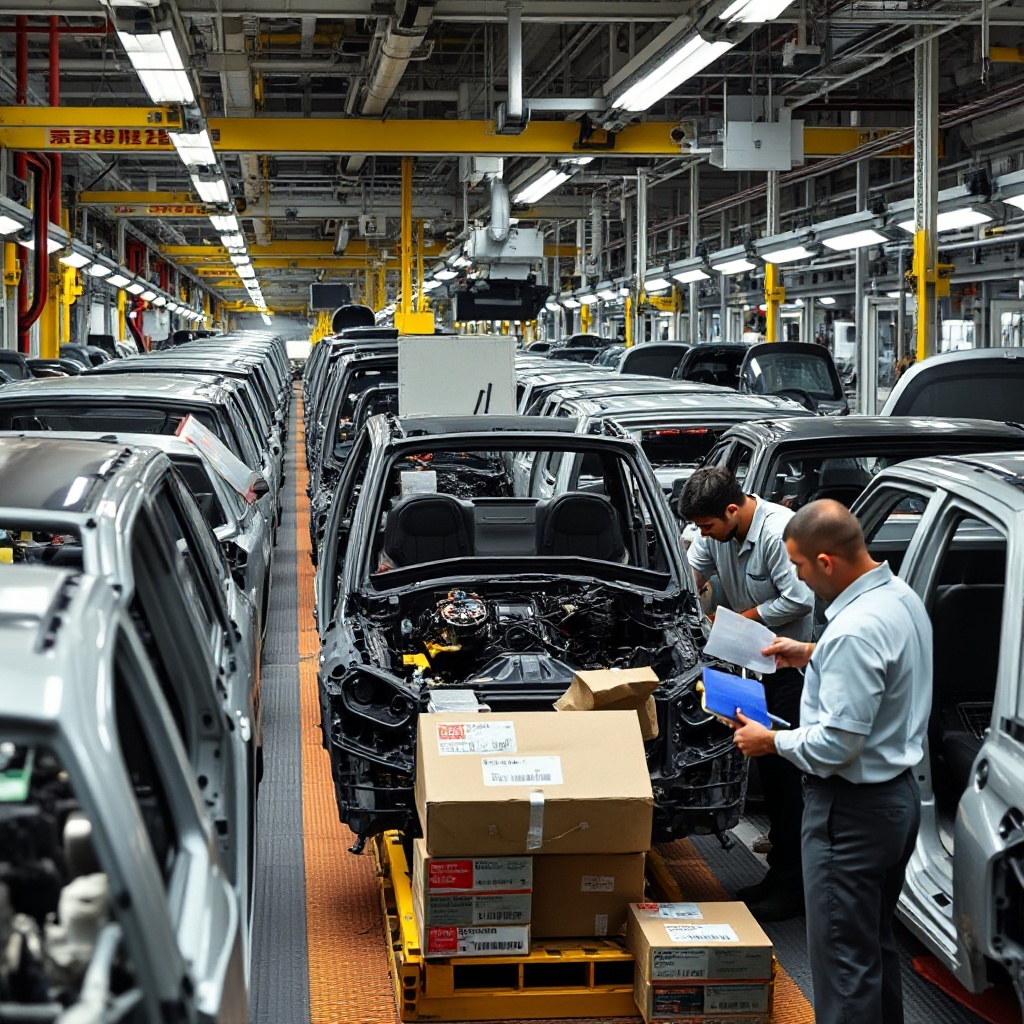
North America's Deeply Interconnected Automotive Ecosystem
The automotive supply chain across North America functions as a single integrated system rather than three separate national industries. Components frequently cross borders multiple times during production, with parts being manufactured, assembled, and refined at specialized facilities throughout the continent before reaching final vehicle assembly.
The scale of this integration is massive:
Nearly half (50%) of U.S. automotive parts imports come from Canada and Mexico
The U.S. imports over $92 billion in automotive goods annually from these neighbors
Total auto parts imports reached $197 billion in 2024, representing a 119% increase since 2008
This intricate network developed over decades as manufacturers pursued efficiency and cost advantages. The result is that no single North American country can independently produce vehicles without significant inputs from its neighbors. A vehicle labeled "Made in America" typically contains substantial foreign content, with components having crossed borders repeatedly during production.
The Vulnerability Gap: How U.S. Automakers Lag Behind Asian Competitors
A troubling competitive disadvantage emerges when comparing U.S. automakers' import dependencies to their Asian counterparts. While American manufacturers face critical supply gaps, companies in Japan and South Korea maintain much lower dependency on external imports for their manufacturing operations.
This difference creates asymmetric vulnerabilities to supply chain disruptions and trade policy changes. Japanese and South Korean automakers have strategically maintained stronger domestic supply networks, giving them greater resilience against geopolitical tensions and shipping disruptions.
Meanwhile, Chinese manufacturing capabilities have surged dramatically. Between 2007 and 2018, China's share of U.S. auto parts imports nearly doubled from 7% to 13%. China has developed the capacity to supply approximately half the global automobile market, creating new dependencies and competitive pressures for American manufacturers.
Tariff Threats and Their Economic Ripple Effects
The prospect of increased tariffs introduces significant complications for U.S. automakers already struggling with import dependencies. Proposed tariffs could reach up to 25% on imported vehicles and auto parts, including those from Canada and Mexico—the very countries most integrated into U.S. supply chains.
Even more modest tariffs would have substantial impacts:
A 10% tariff on imports from Japan, Korea, and Europe would directly affect 16% of U.S. vehicle sales
Steel and aluminum tariffs alone could increase vehicle production costs by 0.43%
Disruptions to the integrated North American production system would cause production delays and reduced competitiveness
These economic consequences extend beyond simple cost increases. The complex supply chains that characterize modern automotive manufacturing make them particularly vulnerable to cascading disruptions, where problems at one point quickly propagate throughout the system.
The Automotive Industry's Economic Significance and Vulnerability
The stakes are extraordinarily high given the automotive sector's outsized economic footprint. The U.S. auto industry contributes nearly 5% to GDP and supports more than 10 million jobs across manufacturing, sales, service, and related industries. Every dollar added in the auto industry multiplies to $4.23 in broader economic value.
This economic engine has already shown signs of vulnerability. Since the mid-1990s, domestic production's share of the U.S. market has declined from a peak of 79% to 65% in 2024. The share of imports in domestic vehicle sales has fluctuated between 41-50% since 2008, representing a substantial shift in production capacity.
Supply chain disruptions could jeopardize the industry's $1.2 trillion economic contribution, with effects extending far beyond the immediate automotive sector into communities nationwide that depend on these manufacturing networks.
The Decline of Domestic Manufacturing Capacity
The current crisis didn't develop overnight but represents the culmination of decades-long shifts in production patterns. U.S. automakers have systematically integrated their supply chains with neighboring countries, leading to a significant decline in domestic manufacturing capacity for critical components.
This trend is particularly acute for newer technologies and components. The electric vehicle transition has highlighted severe domestic manufacturing shortages for batteries, motors, and electronic systems. Many of these components face complete domestic production gaps, forcing reliance on imports that creates strategic vulnerabilities.
Between 2007 and 2018, dependency on Chinese imports nearly doubled, reflecting both China's growing manufacturing capabilities and U.S. companies' pursuit of cost advantages. This trend represents a fundamental restructuring of America's automotive manufacturing base that can't be quickly reversed.
Supply Chain Vulnerabilities in the Electric Vehicle Transition
The automotive industry's ongoing transition to electric vehicles introduces new dimensions to the import dependency problem. EVs require different component sets that face even more severe domestic shortages than traditional vehicle parts.
Critical vulnerabilities exist across the EV supply chain:
Battery minerals like lithium, cobalt, and nickel face significant sourcing challenges domestically
Electronic components and semiconductors for EVs remain predominantly manufactured in Asia
China dominates global EV component supply, creating strategic vulnerabilities for U.S. manufacturers
Automakers are investing in localizing these critical supply chains, but progress remains slow against the scale of the challenge. Without targeted policy intervention, the push toward electric vehicles may further increase import dependency rather than reduce it, exacerbating the existing vulnerabilities.
Strategic Responses to Reduce Import Dependency
Facing these challenges, both industry and government are mobilizing to address the dangerous level of import dependency. Manufacturers are investing in domestic production capacity for critical components, though these efforts face significant lead times before reaching meaningful scale.
Policy responses include:
Trade policy adjustments to incentivize reshoring of critical manufacturing capabilities
Investments in domestic capacity for strategic components, particularly EV batteries
Strategic partnerships to secure supply chains for critical minerals and technologies
National security discussions around protecting essential automotive manufacturing capabilities
The challenge remains balancing cost competitiveness with supply chain security. Domestic production typically involves higher costs than offshore manufacturing, creating difficult tradeoffs between resilience and affordability. Finding this balance will require coordinated efforts between industry and government with a long-term strategic perspective.
Sources:
Statista - Does the U.S. Auto Industry Need Protection?
Z2Data - How Dependent Automotive Industry on Electronic Components Manufactured China
Alliance for Automotive Innovation - DATA DRIVEN Report
S&P Global Mobility - Automotive Industry Forecast 2025 Tariffs EVs