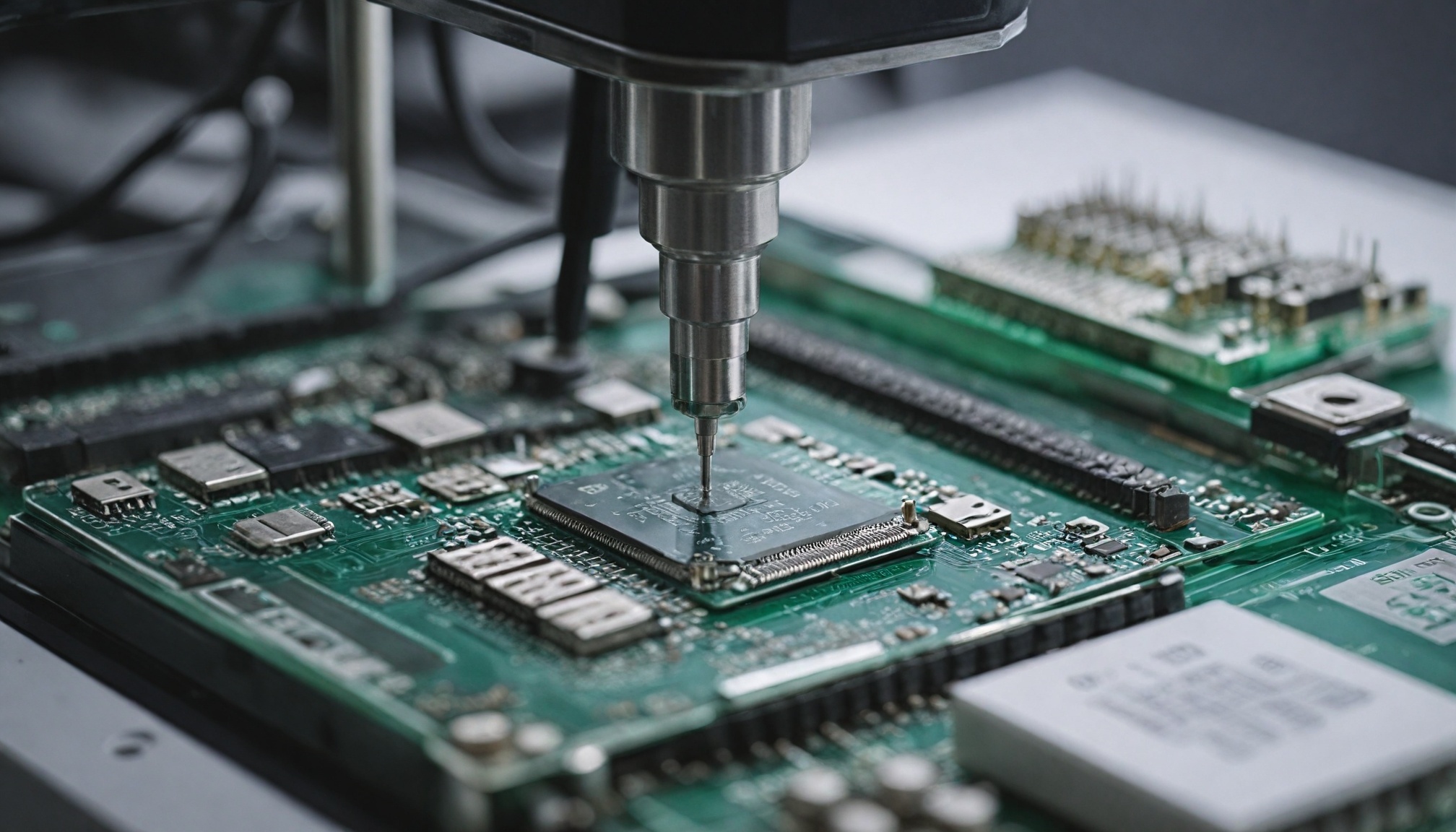
Raspberry Pi improves manufacturing with intrusive reflow soldering, cutting returns by 50%, reducing CO₂ emissions, and streamlining production through innovative PCB assembly techniques.
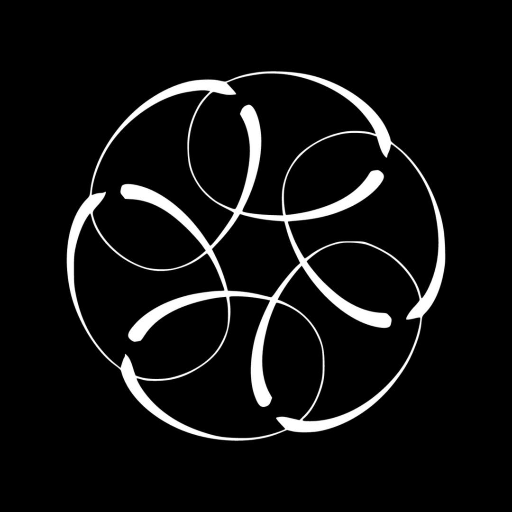
Drivetech Partners
Intrusive reflow soldering has transformed Raspberry Pi's manufacturing process, allowing through-hole connectors to be placed with the same machines used for surface-mount components—eliminating separate soldering steps and specialized robotics. This innovative technique has produced remarkable improvements: cutting product returns in half, reducing manufacturing time by 15%, and eliminating 43 tonnes of CO₂ emissions annually, demonstrating how small production changes can dramatically improve quality while reducing environmental impact.
Key Takeaways
Intrusive reflow soldering has cut product returns by 50% while reducing manufacturing time by 15%
The streamlined process eliminates 43 tonnes of CO₂ emissions annually by removing separate soldering steps
This technique allows both through-hole and surface-mount components to be placed by the same machines
Implementation required close collaboration between Raspberry Pi and Sony UK Technology Centre
The successful application demonstrates how small manufacturing changes can yield substantial quality and environmental benefits
Raspberry Pi's Manufacturing Revolution: Intrusive Reflow Soldering
The evolution of electronics manufacturing often happens through incremental but transformative innovations. Raspberry Pi's adoption of intrusive reflow soldering represents precisely such a breakthrough—a relatively simple concept that has dramatically changed how their popular single-board computers are manufactured. The technique, implemented for the Raspberry Pi 5, has created a more efficient production process while significantly improving product quality.
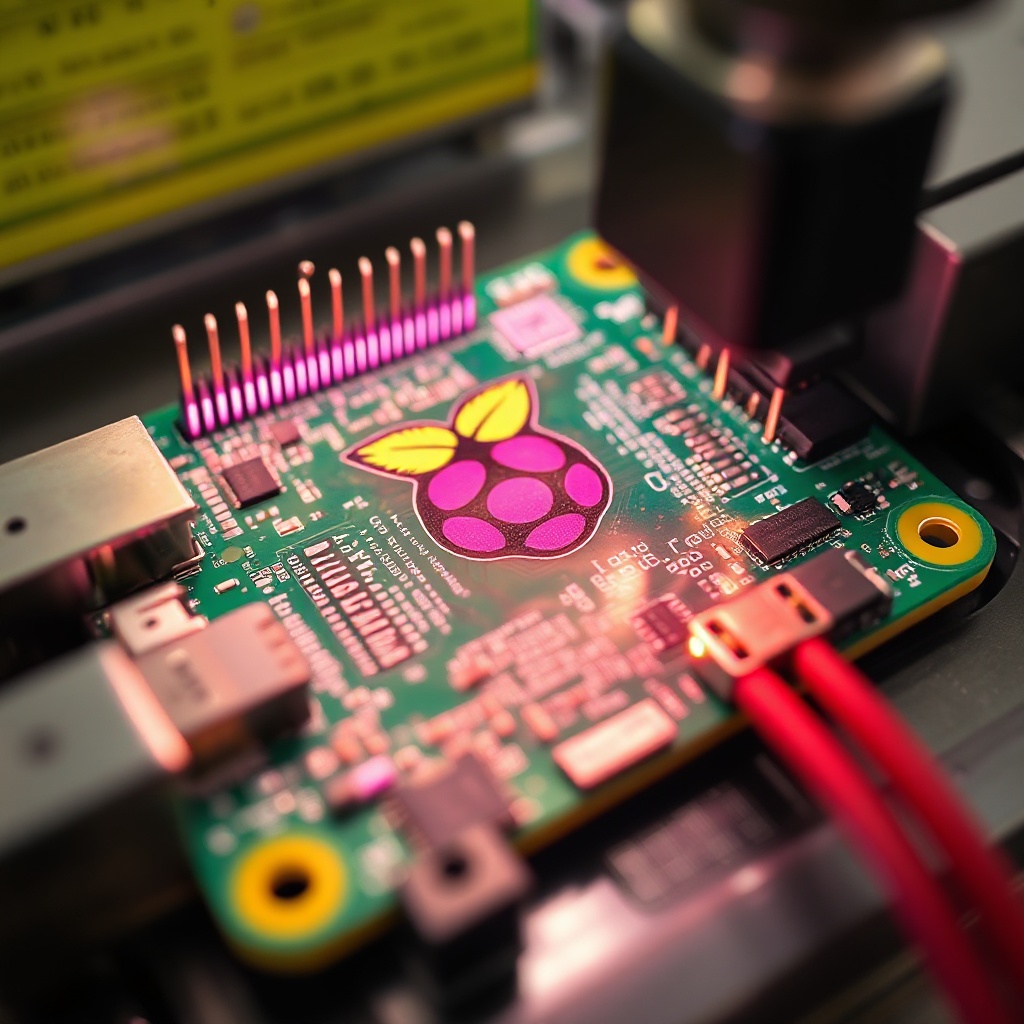
The results speak for themselves: product returns cut by half, manufacturing time reduced by 15%, and annual carbon emissions decreased by 43 tonnes. These impressive figures highlight how production process refinements can create cascading benefits across quality, efficiency, and sustainability metrics.
What Is Intrusive Reflow Soldering? Understanding the Innovation
Intrusive reflow soldering (also known as pin-in-paste soldering) is a technique that simplifies PCB assembly by allowing through-hole connectors to be placed using the same pick-and-place machines that handle surface-mount components. This approach eliminates the need for a separate wave soldering step and specialized through-hole component placement robotics.
The process works through several key steps:
Applying solder paste to both surface-mount pads and through-holes on the PCB
Using automated pick-and-place machines to position all components—both surface-mount and through-hole
Running the entire board through a single reflow oven cycle, where heat melts the solder paste to create secure connections
This consolidated approach creates a more streamlined production flow that reduces complexity and potential points of failure in the manufacturing process.
Before and After: Streamlining the Manufacturing Process
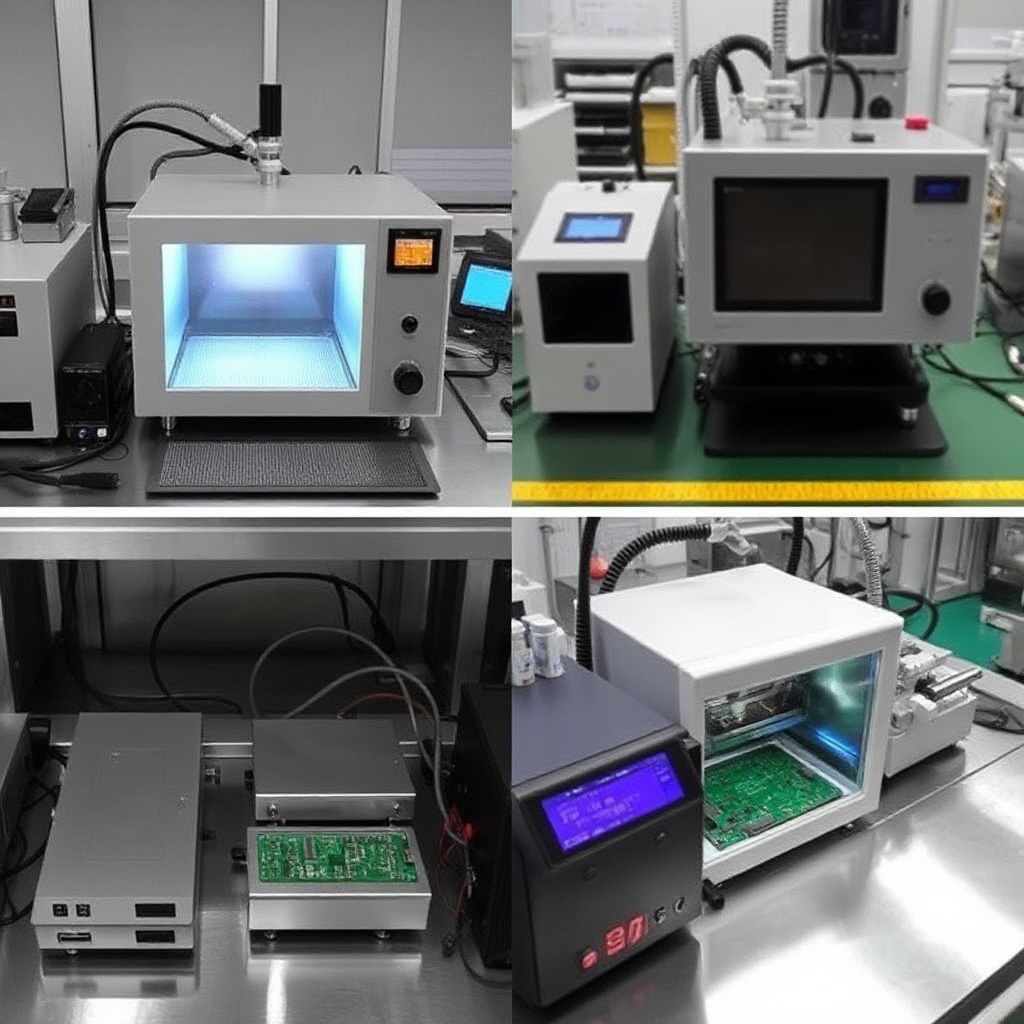
The traditional manufacturing process for boards with mixed component types like the Raspberry Pi required multiple separate production stages. Surface-mount components would be placed by automated machines and soldered in a reflow oven, while through-hole components required either manual insertion or specialized robots, followed by a separate wave soldering process.
This multi-step approach created several inefficiencies:
Increased handling between processes, risking damage to components
Greater equipment requirements, including wave soldering machines
Extended production time due to separate processing steps
Higher energy consumption from running multiple soldering systems
With intrusive reflow soldering, the entire process has been consolidated into a single flow. All components are placed by the same machines and soldered in one pass through the reflow oven, dramatically simplifying production while improving consistency.
Technical Implementation: Making Intrusive Reflow Work
Implementing intrusive reflow soldering required careful technical refinements to ensure reliable connections for all components. The team at Raspberry Pi, in collaboration with Sony's manufacturing experts, worked through several technical challenges to perfect the process.
Key technical enhancements included:
Overprinting and double printing of solder paste to ensure adequate volume for through-hole connections
Custom stencil designs that deposit precise amounts of solder paste around through-hole connections
Modifications to PCB layout to optimize for the new soldering technique
Adjustments to connector designs to improve compatibility with the process
These technical refinements were essential to achieving the high-quality, consistent solder joints necessary for reliable product performance. The iterative development process eventually yielded a manufacturing method that produced superior results compared to the previous approach.
Environmental Impact: Quantifying Sustainability Gains
The environmental benefits of the new manufacturing process extend beyond the headline figure of 43 tonnes of CO₂ eliminated annually. Raspberry Pi conducts detailed Life Cycle Assessments according to Greenhouse Gas Protocol and ISO 14044:2006 standards to accurately measure their environmental impact.
The sustainability improvements come from multiple sources:
Elimination of the energy-intensive wave soldering process
Reduced need for transportation between manufacturing stages
Decreased requirement for specialized equipment
Lower material waste from improved first-pass yield
These combined factors create a significantly lighter environmental footprint for each Raspberry Pi manufactured, aligning with the company's commitment to sustainable production methods.
The Power of Partnership: Raspberry Pi and Sony Collaboration
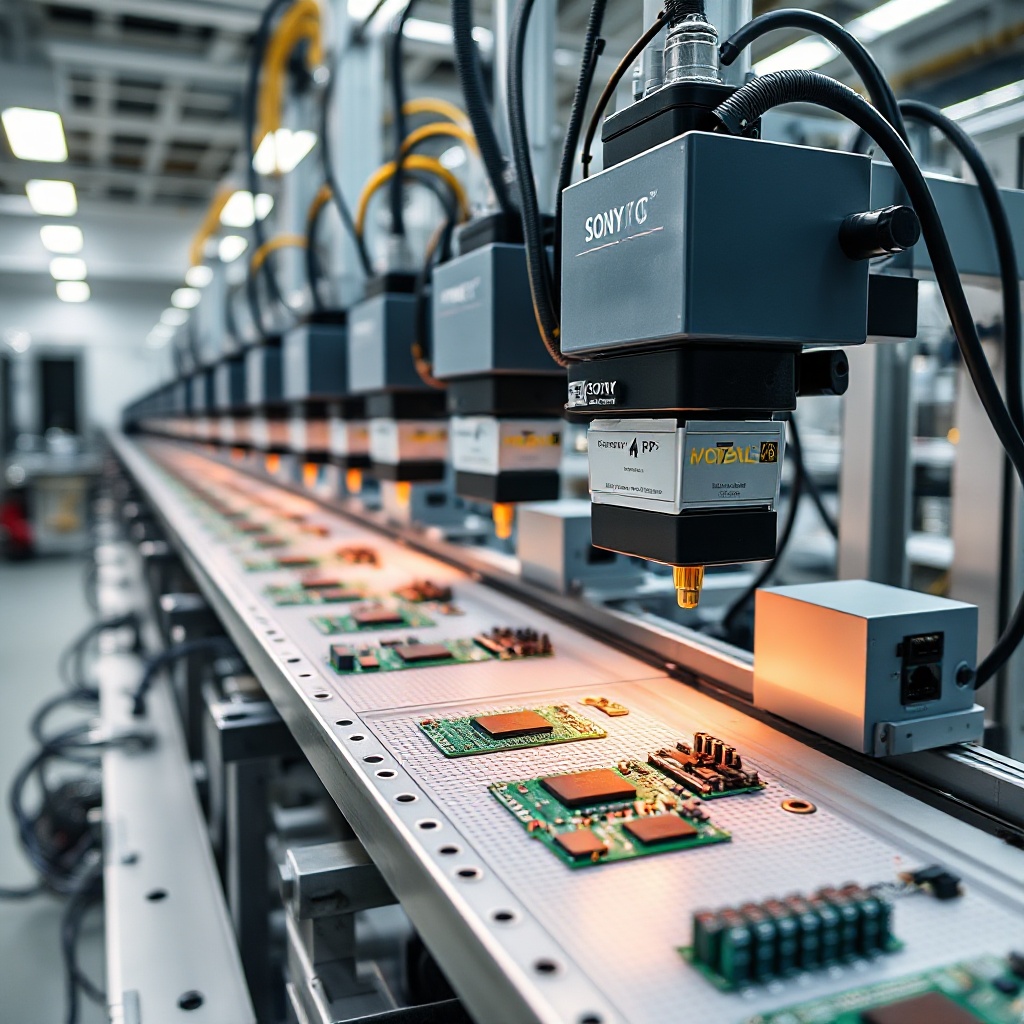
The successful implementation of intrusive reflow soldering on the Raspberry Pi 5 represents the latest achievement in a decade-long manufacturing partnership between Raspberry Pi and Sony UK Technology Centre. Since 2012, Sony UK TEC has manufactured over 50 million Raspberry Pi units, with the relationship continuing to drive innovation in production techniques.
This collaborative approach allowed teams from both companies to work closely on:
Adapting PCB designs for optimal compatibility with the new process
Refining component specifications to ensure reliable soldering
Developing inspection methodologies to verify joint quality
Testing and iterating on process parameters to maximize yield
The partnership demonstrates how shared technical expertise between a product designer and manufacturing partner can drive meaningful innovations in production processes.
Industry Implications: Small Changes, Big Results
The success of intrusive reflow soldering at Raspberry Pi carries important lessons for the broader electronics manufacturing industry. It demonstrates how focused process improvements can simultaneously address quality, efficiency, and sustainability challenges without requiring complete production line overhauls.
Key takeaways for other manufacturers include:
Process simplification often yields benefits across multiple metrics
Environmental improvements can align with business goals like cost reduction and quality improvement
Established technologies can be adapted in innovative ways to solve manufacturing challenges
Close collaboration between design and manufacturing teams enables process innovations
As electronics manufacturers face increasing pressure to reduce environmental impact while improving quality and managing costs, the Raspberry Pi example provides a compelling case study in how thoughtful process innovation can help meet these seemingly competing demands.
By implementing intrusive reflow soldering, Raspberry Pi has set a new standard for efficient, high-quality, and environmentally responsible electronics manufacturing—proving that sometimes the most impactful innovations come from rethinking existing processes rather than inventing entirely new technologies.
Sources
Globalwell PCBA: Guide to Intrusive Soldering
Sony UK Technology Centre: The Latest Raspberry Pi 5 Rolls Off Production Lines at Sony UK TEC