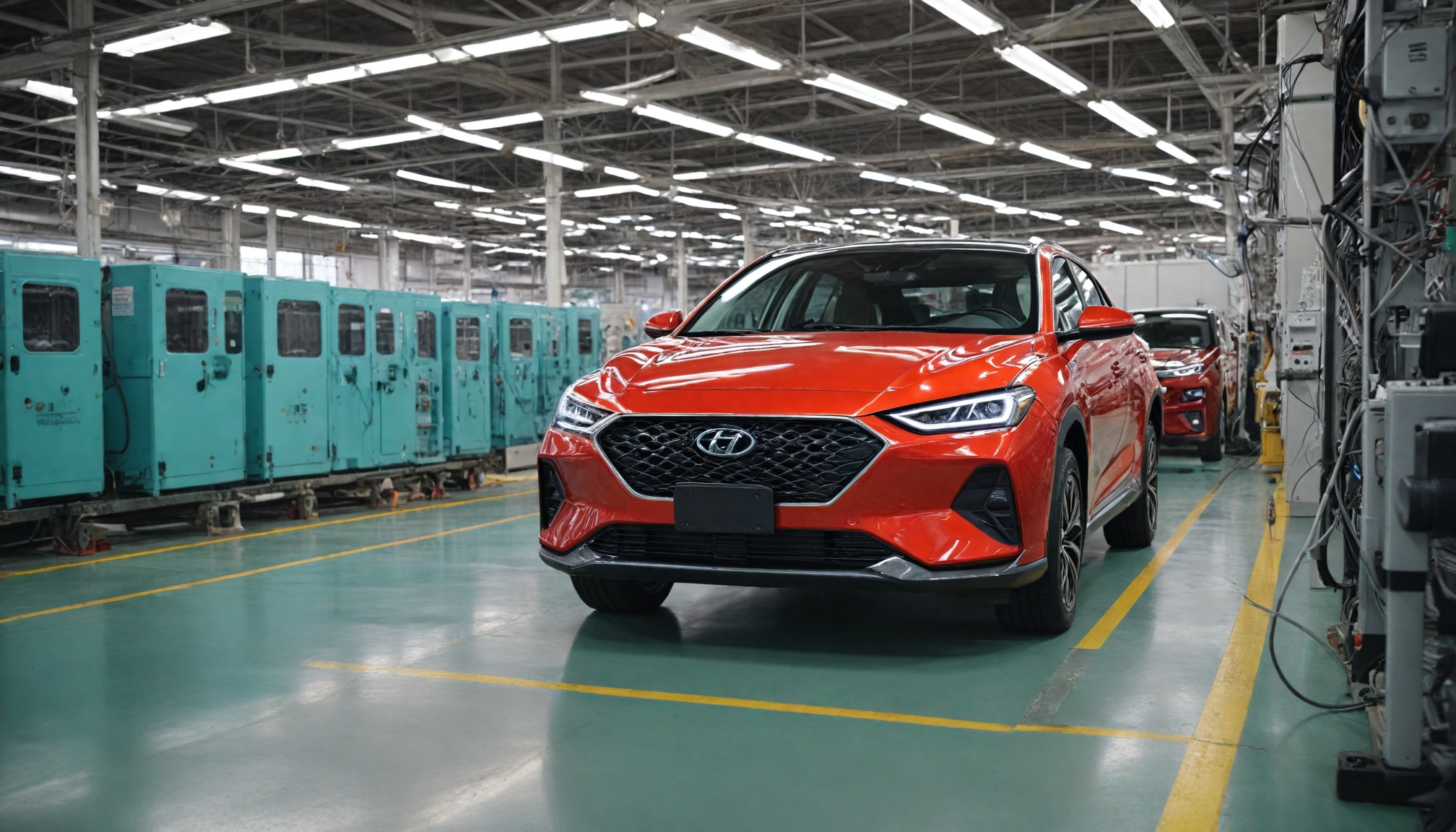
China's EV sector transforms as BYD leads vertical integration revolution, controlling everything from semiconductors to batteries, challenging global automotive business models and setting new standards.
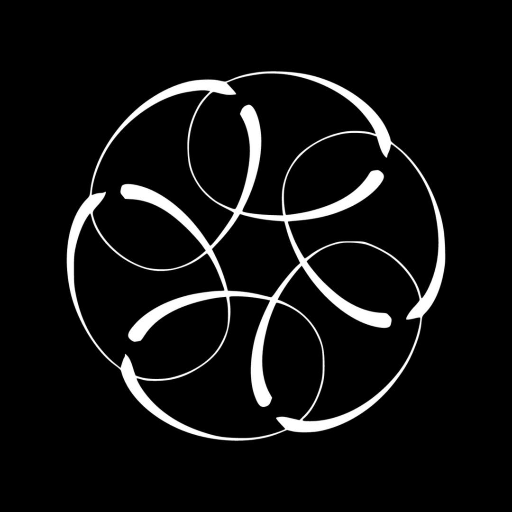
Drivetech Partners
China's EV sector is undergoing a transformative shift as companies like BYD pursue aggressive vertical integration strategies, controlling everything from semiconductor production to battery manufacturing in their quest to dominate the global electric vehicle market. This approach has created a new competitive paradigm where Chinese manufacturers increasingly set the standards for innovation speed, manufacturing efficiency, and cost structure, challenging traditional automotive business models worldwide.
Key Takeaways
BYD leads China's vertical integration revolution with in-house component production, controlling critical technologies from batteries to semiconductors
Chinese battery giants CATL and BYD together command 55.4% of global market share, demonstrating China's dominance in the EV supply chain
BYD's vertical integration provides exceptional supply chain resilience, reducing vulnerability to external disruptions while accelerating innovation cycles
Ongoing price wars and industry consolidation favor large-scale integrated manufacturers, squeezing out smaller players and challenging foreign competitors
Western automakers and governments face difficult decisions about decoupling from Chinese suppliers despite significant cost and scale disadvantages
China's EV Giants Consolidate Power Through Component Control
BYD has aggressively positioned itself at the forefront of a fundamental shift in how electric vehicles are designed, built, and supplied. Unlike traditional automakers who rely heavily on external supplier networks, BYD has pursued comprehensive vertical integration across the entire EV value chain. This strategy encompasses everything from raw material sourcing to final vehicle assembly.
At the heart of this approach is BYD's in-house production of critical components through subsidiaries like BYD Semiconductor. The company's "Blade Battery" technology, launched in 2020, exemplifies the benefits of this integrated approach. By late 2022, BYD had achieved a remarkable 135 GWh production capacity for these batteries, enabling significant advantages in safety, energy density, and cost leadership.
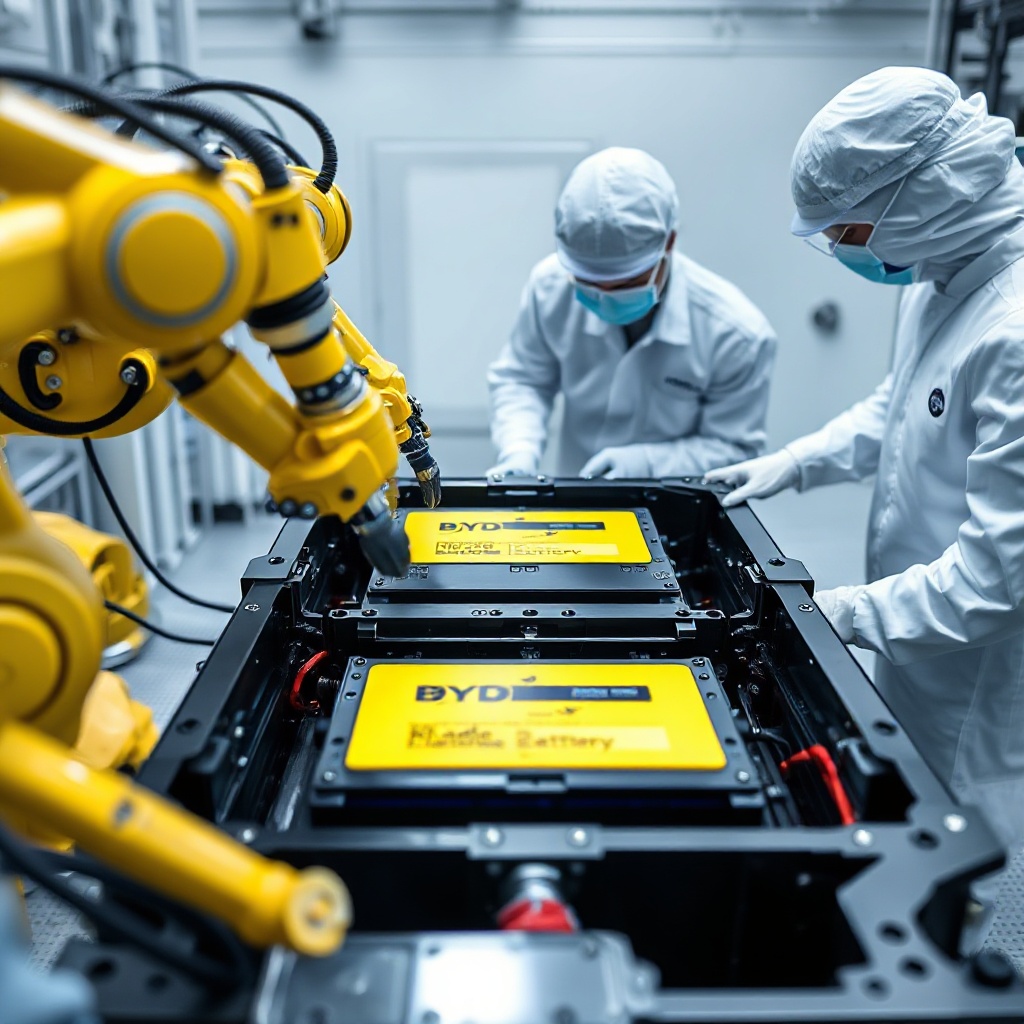
Chinese battery manufacturers now dominate global supply chains. CATL leads with 38.1% of global EV battery installations, followed by BYD at 17.3%. Together, these two Chinese companies control 55.4% of the global market (Jan-Apr 2025). This concentration of power stands in stark contrast to Tesla and Western automakers who typically depend on external supplier relationships.
Market Dominance: Chinese Players Eclipse Foreign Competition
The results of this strategic approach are evident in market performance data. BYD has established itself as the undisputed leader in China's New Energy Vehicle (NEV) market with a commanding 28.5-28.9% share in 2025. This puts BYD far ahead of competitors like Geely (13.1%), Changan, Leapmotor, and Tesla.
BYD's sales trajectory continues to impress with 293,021 units sold in May 2025 (representing a 9.2% year-over-year increase) and a total of 1,257,961 units from January to May 2025. Meanwhile, Tesla's position in the Chinese market has weakened considerably, with its market share declining to just 4.6% for Jan-May 2025, continuing a multi-year downward trend.
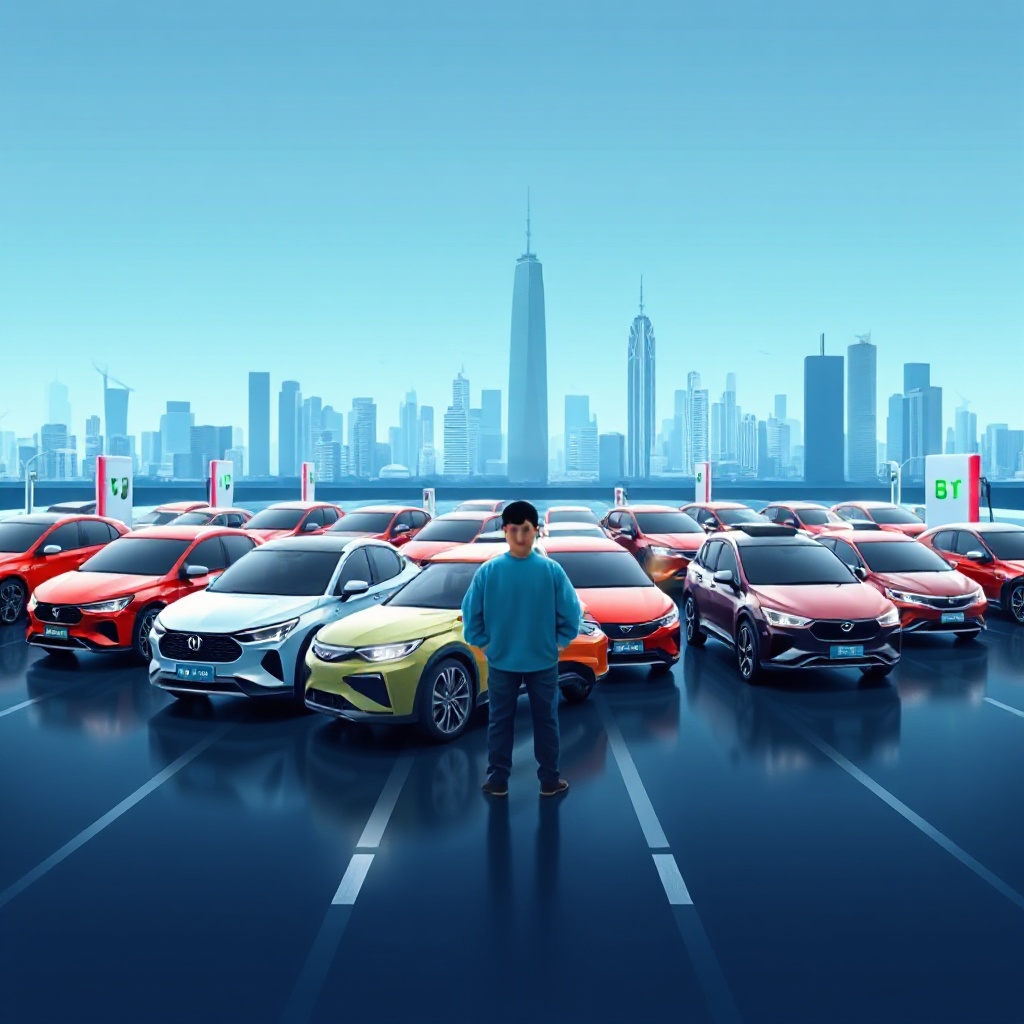
China's dominance extends beyond its domestic market. The country produced 62% of the world's EVs in 2022, with projections to produce over 10 million NEVs in 2024. Industry analysts predict that Chinese NEVs will account for more than 70% of annual new vehicle sales by 2030, cementing China's position as the global epicenter of electric transportation.
Price Wars and Consolidation: The Industry Shakeout
BYD's scale and cost advantages have enabled an aggressive pricing strategy that has triggered an industry-wide EV price war in China. This competitive environment has compressed margins across the sector, putting enormous pressure on smaller manufacturers and even affecting BYD itself, which lost $21.5 billion in market value since late May 2025 due to these competitive tactics and broader market uncertainty.
The Chinese EV market is experiencing significant overcapacity combined with weaker-than-expected demand, accelerating an industry consolidation that favors efficient, vertically integrated players. Despite government interventions to support the sector, only large-scale, cost-efficient manufacturers like BYD and CATL appear positioned to weather this inevitable industry shakeout.
A key factor in BYD's resilience is its e-Platform 3.0 standardization strategy. This approach enables rapid model launches, extensive component sharing across product lines, and sustained cost leadership even during pricing pressures. This standardization represents a fundamental competitive advantage that few competitors can match.
Supply Chain Resilience Through Vertical Integration
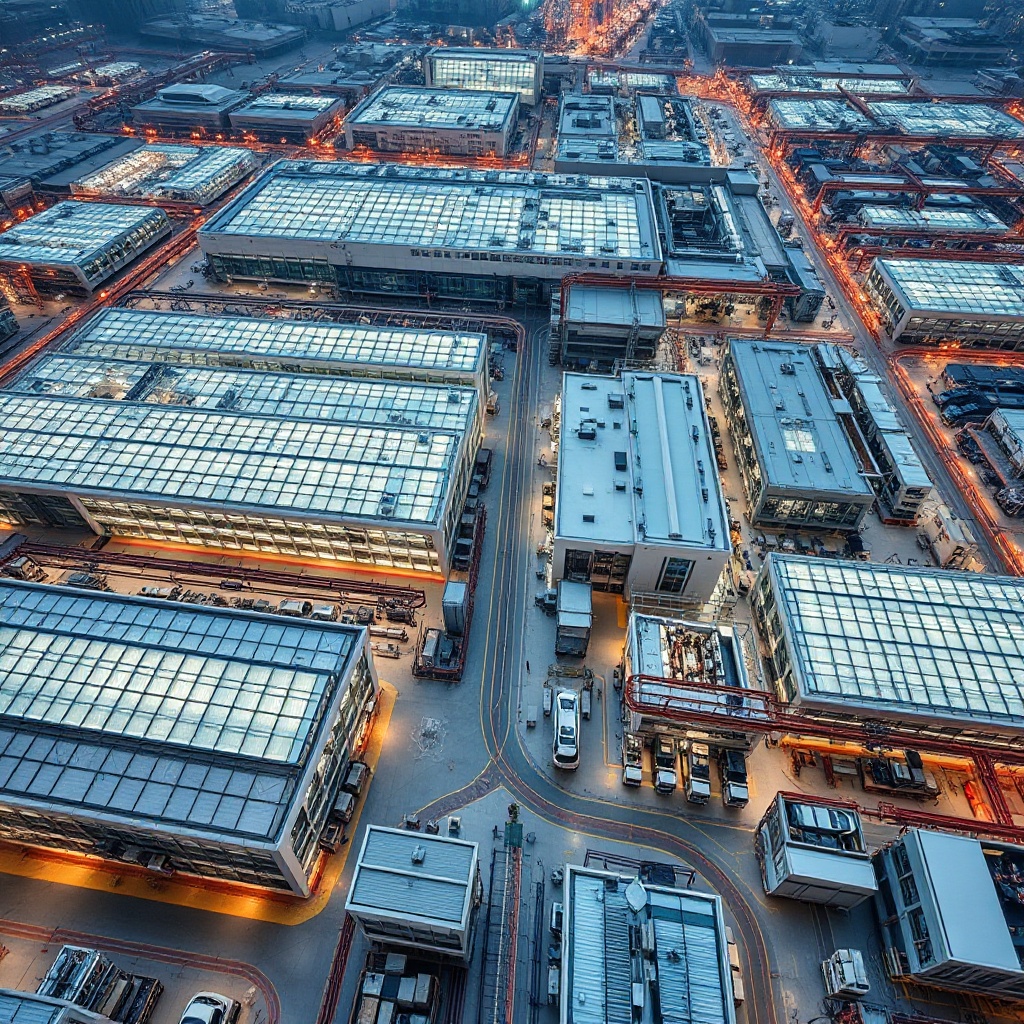
BYD's control of in-house component production significantly reduces vulnerability to external supply shocks, price volatility, and supply chain disruptions that have plagued many global automakers. By maintaining control over batteries—which can represent up to 40% of an EV's total cost—BYD gains significant pricing power and supply security that competitors lack.
The company has implemented extensive automation and standardization through robotic handling and modular design throughout its manufacturing facilities. This approach ensures consistent quality while allowing for rapid adaptation to demand fluctuations with minimal dependence on external suppliers.
This supply chain control provides a stark contrast to traditional automakers' vulnerability to global supplier networks and bottlenecks. During recent global supply chain crises, BYD's self-sufficient production model allowed it to maintain production levels while competitors struggled with semiconductor shortages and logistics challenges.
Innovation Acceleration: Competitive Advantages of Integration
One of the most significant benefits of BYD's vertical integration is the acceleration of innovation cycles. By coordinating R&D across battery, motor, and electronics divisions, the company can develop integrated technological solutions faster than competitors relying on separate supplier innovation timelines.
BYD's cell-to-pack and Blade Battery innovations demonstrate how in-house development leads to market-differentiating technologies. These innovations might have taken years to implement in traditional OEM-supplier relationships but were rapidly deployed throughout BYD's product lineup.
Platform standardization through e-Platform 3.0 further accelerates new model development while maintaining cost efficiency. This approach allows BYD to implement innovations across product lines without lengthy supplier negotiations or contracts. The direct feedback loops between manufacturing and R&D enable continuous improvement cycles that further enhance BYD's competitive position.
Foreign Suppliers Face Existential Challenges
Western and Japanese suppliers find themselves increasingly squeezed out of the Chinese market as domestic OEMs favor in-house production or local suppliers. Foreign brands are losing market share in China as domestic manufacturers capture most market growth, creating a challenging environment for non-Chinese companies.
Western governments pushing to decouple from Chinese battery and component supply chains face significant challenges due to China's scale and cost advantages. This creates a difficult dilemma for foreign suppliers: either localize within China (risking technology transfer) or lose access to the world's largest EV market.
The manufacturing scale achieved by Chinese companies creates price points that foreign competitors struggle to match without similar vertical integration strategies. This cost disadvantage is becoming increasingly difficult to overcome, even with government subsidies or trade protections in Western markets.
Global Implications: The New Competitive Baseline
China's vertically integrated model is becoming the new global standard for EV manufacturing efficiency and innovation speed. Western automakers must adapt to rapid product cycles, platform modularity, and integrated manufacturing to remain competitive in this transformed industry landscape.
Chinese firms are increasingly setting global technological standards in batteries, motors, and manufacturing techniques. This leadership position allows them to define the direction of the industry and forces competitors to follow rather than lead innovation cycles.
The global industry faces a difficult choice: partner with Chinese suppliers (risking dependence) or invest heavily in alternative supply chains at higher costs. Competition is increasingly based on complete ecosystem control rather than traditional vehicle manufacturing excellence, requiring fundamental rethinking of automotive business models.
As this new paradigm solidifies, companies that fail to adapt to these integrated manufacturing approaches may find themselves permanently disadvantaged in the global race for EV market share and technological leadership.
Sources
CleanTechnica - 53% EV Share in China — May 2025 Sales Report
CnEVPost - Automakers' share of China NEV market in May: BYD No. 1 with 28.5%
Fortune - BYD unleashes an EV industry reckoning that alarms Beijing
Automotive Manufacturing Solutions - From battery maker to EV leader: BYD's strategic rise
CnEVPost - Global EV battery market share in Jan-Apr 2025: CATL 38.1%, BYD 17.3%